Introduction
In the rice milling process, cleaning paddy is the first and most crucial step. Cleaning not only ensures the quality of the final rice but also supports and protects the subsequent processing stages. Today, let’s explore more about paddy cleaning together!
Paddy cleaning process
The process of cleaning raw grains is complex, and we will use many paddy cleaners to help us achieve the cleaning standards. The cleaning process of paddy usually includes the following important steps.
Initial Cleaning
The initial cleaning stage mainly helps remove most of the large impurities in the paddy, such as straw, rice heads, weeds, etc. This stage effectively removes these large impurities and prepares the paddy for further processing.
In this stage, we generally use a cylinder initial cleaning sieve. It utilizes the difference in size between the grains and impurities. Rotating two inclined sieves can help you separate large impurities larger than the inner sieve holes and small impurities smaller than the outer sieve holes. The cylinder initial cleaning sieve is particularly suitable for cleaning paddy with large impurities. It has excellent screening performance and a high impurity removal rate, and the rotating sieve effectively prevents clean grains from being mixed with impurities. It also has low power consumption and high output, making it ideal for cleaning paddy of various capacities.
Detailed Cleaning
This stage mainly helps remove small impurities in the paddy, such as broken husks, dust, etc., to further clean the impurities in the rice. At this point, finer screening or vibration equipment is needed. In this stage, you will typically use a gyratory vibrating screen and a vibration cleaning screen. They have similarities but also differences in some aspects.
The gyratory vibrating screen mainly uses the circular motion of the screen body to automatically grade the material. It separates large and small impurities using screens with varying mesh sizes, from large to small. The vibration cleaning screen, on the other hand, uses high-frequency vibration and horizontal cyclic motion of the screen body to effectively classify the material by particle size. It also uses screens with mesh sizes ranging from large to small to separate impurities.
In general, the gyratory vibrating screen is suitable for paddy with medium impurity content, while the vibration cleaning screen is better suited for finer paddy with more types of impurities.
The stone removal
This stage is aimed at removing stones and gravel from the paddy. These impurities not only affect the quality of the rice but can also cause varying degrees of damage to subsequent processing equipment. Therefore, the stone removal is essential.
So in this step, you need a specific gravity stoner. This machine takes advantage of the difference in specific gravity between paddy and stones. It separates the stones using screen vibration and suction. On the scale-like plates, the raw grain is in a suspended or semi-suspended state, with the paddy on the top layer and the stones at the bottom. The scale-like plates prevent the stones from sliding down. Due to vibration and inertia, the stones gradually move backward, ultimately achieving the stoning effect.
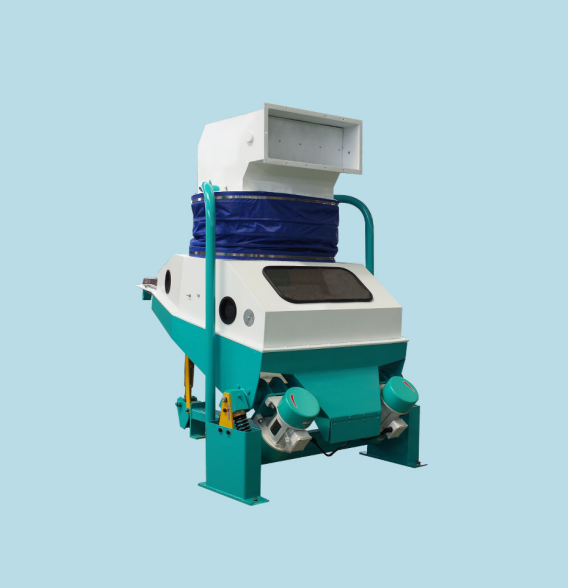
Why important?
The cleaning of grain requires such a complex process, so why is cleaning raw paddy so important? The main reasons are as follows:
Remove impurities
First, after harvest, paddy rice contains various impurities, such as dust, husks, weeds, straw, and pests. These impurities can affect the quality and appearance of the rice. The cleaning process helps remove these impurities and improve the quality of the rice.
Increase productivity
Secondly, the cleaning process can help you remove the large and hard impurities, reducing the failure rate of subsequent processing equipment. It prevents downtime caused by impurities, helping you to improve overall production efficiency.
Protect subsequent processing equipment
Thirdly, in the rice milling production line, large impurities may clog the processing line, and stones can directly damage machines like rice huskers and rice whitening. By cleaning the paddy before processing, you can remove impurities and protect your equipment, extending the lifespan of the entire production line.
Ensure food safety
Last but not least, the cleaning process also helps you remove damaged paddy, dust, stones, and pests, ensuring hygiene and safety while improving the edibility of the rice.
How to choose your paddy cleaning machine?
The cleaning process mentioned above can be omitted depending on the production situation. Correspondingly, not all cleaning machines are necessary. Considering the following factors can help you choose the right machines to achieve the best cleaning results based on your specific needs.
Rice impurity situation
First, you can choose the machines according to the impurity level in your paddy. For example, if your rice contains a high level of large impurities, you can use the cylinder initial cleaning sieve. If there are many different types of impurities, you can use the vibration cleaning sieve, which uses high-frequency vibration to help remove various impurities. Its sorting efficiency is higher and can achieve greater precision in cleaning.
Capacity
Next, you need to consider your production capacity requirements. The cylinder initial cleaning sieve has a wide range of capacities and is suitable for cleaning grains of all capacities. The vibration-cleaning sieve is ideal for high-capacity paddy with many types of impurities, so it is used in rice milling lines with a capacity of 40 tons or more. As production capacity increases, you can add more cylinder initial cleaning sieves to help ease the cleaning pressure.
Budget
Finally, you have to consider your budget. If your budget is limited, you can start by purchasing core equipment, such as the cylindrical initial cleaning sieve and the specific gravity stoner. The cylindrical initial cleaning screen and the specific gravity stoner removal machine can be combined to form a combined cleaning screen. If there is a need for upgrades later, you can purchase additional equipment. This approach can help ease your financial pressure.
Conclusion
The paddy cleaning process before milling is a complex and meticulous step, involving various equipment and procedures. By properly configuring cleaning machines, we ensure the required cleanliness and improve production efficiency. ANON Farm Equipment is dedicated to recommending the most suitable machines for each customer and optimizing their production process. ANON, Easy operate, Harvest more.
FAQ
1. Why is it important to dry the rice before milling?
Proper drying technique to reduce moisture content in rough rice is a key factor in improving milling quality. Sun drying usually increases broken rice percentage, if drying is conducted for a whole day. If the temperature of the grain gets too high, head rice recovery is reduced.
2. What is paddy cleaner?
Paddy cleaner is suitable for removing all sizes of impurities and stones from wheat, paddy, corn, and oil plants. Reasonable design, small volume, reliable operation, low energy consumption, good cleaning effect, and long service life.
3. What are the methods of grain cleaning?
This is done by various methods such as sieving, stripping, dust removal, and aspiration. The aim is to free the grain from all impurities that can affect the quality of the end product.
What is the grain clean standard?
4. What is Grain clean?
The most common cleanliness requirement for bulk carriers is that of grain clean. It means “clean, swept, washed down by fresh water and free from insects, odor, the residue of previous cargo (incl. coal, clinker.)/loose rust scale/paint flakes, etc.