Introduction
The agricultural market is very competitive today. Have you thought about how to increase crop yields while lowering costs? Combine harvesters are important tools because they are efficient and require less labor. This article will explain how a combine harvester works, the different types available, and what to consider when buying one. I hope this helps you!
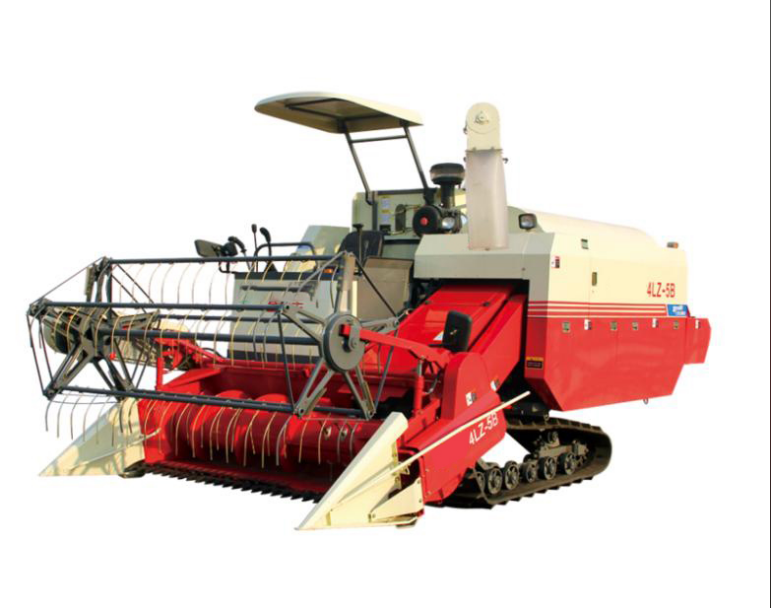
combine harvester
What is a Combine Harvester
A combine harvesting machine, also known as a grain combine, is a machine that can harvest, thresh, separate, clean, and collect grain all at once. It helps turn your field crops into grains. Using a combine harvesting machine can reduce losses by 5% to 8% compared to traditional manual harvesting. It also saves you labor when bundling, moving, and feeding during threshing, greatly easing your workload.
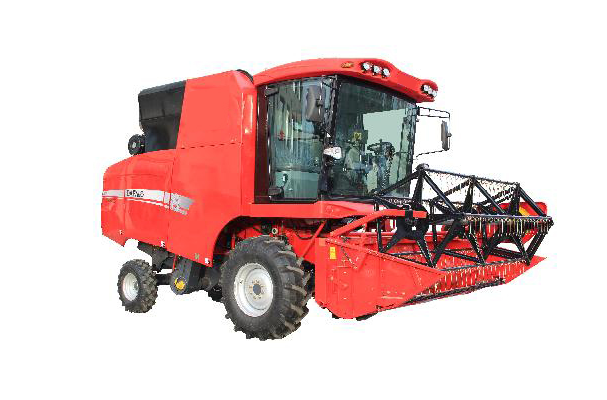
combine harvester
Components of a Combine Harvester
Different types of combine harvesters have different designs. Here, we’ll take the fully-fed combine harvesting machine as an example to explain its main parts.
Grain Divider
The grain divider is installed on both sides of the combine harvesting machine. When it contacts the crops, it separates the crops ready for harvest from those that are not, guiding the crops into the cutter bar.
Reel
The reel is located above the cutter bar and has a pentagon shape. It supports the uncut crops and lays the cut crops onto the cutting platform. The speed and position of the reel need to be adjusted based on the growth of your crops to ensure effective handling and transport.
Cutter Bar
The cutter bar is at the front of the machine. It usually consists of a series of alternating blade-like cutters. These blades move back and forth quickly, driven by a high-speed shaft, effectively cutting the grain stalks without damaging the grains.
Conveyor
The auger is located at the back of the cutter bar. It moves the cut crops, which are laid out on the platform, toward the conveyor entrance using spiral blades. Then, a telescoping arm feeds the crops into the conveyor channel.
Threshing Cylinder
The threshing cylinder is the main threshing part of the combine harvesting machine. It rotates to hit and rub the crops using structures like bars or spikes. The speed of the cylinder needs to be adjusted based on the type of crop and its moisture level.
Concave Plate Sieves
The concave plate sieves have holes that allow the grains to pass through while trapping larger impurities, like stems. To ensure the grains can separate easily, the gap in the concave plate sieves should also be adjusted based on the type of crop.
Clear Selection Sieve
The clean selection sieve includes upper and lower screens, which mainly use vibrations to further remove impurities from the grains, like chaff and broken straw. Different sizes and shapes of holes can filter out different impurities. By adjusting the screen’s angle and vibration frequency, you can improve the cleaning process.
Fan
The fan provides airflow for cleaning. By adjusting the fan’s speed and direction, light impurities on the cleaning screen can be blown away, leaving clean grains on the screen.
Auger
The auger lifts the cleaned grains to the storage bin for stacking.
Grain Tank
The storage bin is used to temporarily hold the cleaned grains.
How Does a Combine Harvester Work?
To clearly explain how a combine harvester works, I will break down its steps into cutting, threshing, separating, storing, and straw handling. I will use a fully-fed combine harvester as an example.
Cutting
When the combine harvester enters the field, the divider separates the unharvested crops from those ready to be harvested. The feeding auger helps guide the crops to the cutter bar, where the crops are cut. After cutting, the feeding auger lays the crops flat on the platform.
Threshing
The spiral guide fins on both sides of the auger transport the crops to the middle of the cutter bar. The telescoping teeth in the middle push the crops onto the inclined conveyor bridge, which then carries the crops to the drum.
Inside the cylinder, metal rods hit and rub the incoming crops, causing the grains to fall off the heads, while the straw is expelled from the back of the cylinder.
Grains, broken straw, chaff, and other debris fall through the concave plate sieves into the vibrating screen. The shaking sieve separates larger impurities, while the rotor and sieve further separate the grains from the straw. The sieve sorts the grains and larger impurities by size, and the fan uses airflow to blow away the lightweight chaff. The rotor spins quickly, creating centrifugal force to further separate the grains from the impurities.
Winnowing
The clean grains reach the cleaning system, where the fan and vibrating screen play important roles. The fan blows away the lighter impurities, while the vibrating screen further sorts the grains, ensuring that only clean grains go into the storage bin. The grain mixture moves onto a slide and enters the re-threshing and cleaning device for further processing.
Storage
The cleaned grains slide down the chute to the grain auger and are finally lifted to the storage bin by a scraper elevator. However, the storage bin is only for temporary storage. To improve efficiency, I recommend using a trailer to unload the clean grains while you are harvesting.
Straw management
A fully-fed combine harvesting machine uses cutting and throwing devices to handle the straw. After the straw separates from the grains, the machine moves it to the back of the drum, where it chops and evenly spreads it back onto the field. This allows the straw to return to the soil and serve as fertilizer.
Types of Combine Harvesters
When classifying combine harvesters, the harvesting method, walking method, power configuration, and threshing device structure are often used as the basis for classification. Next, I will explain these types of harvesters to you.
According to the Reaping Method
Based on the feeding method, combine harvesting machines can be divided into fully-fed and half-fed types.
Half-feed Combine Harvester
A half-feed combine harvester means only the heads of the crops enter the threshing drum. This design allows for higher efficiency and lower loss rates, with lower power consumption. It also helps keep the straw intact, resulting in a total grain loss rate of less than 2.5% and an impurity rate of less than 0.5%.
The structure for conveying and cutting crops in a half-fed combine harvesting machine includes a feeding finger and a straw-holding chain. This design is more complex, which makes the production cost higher.
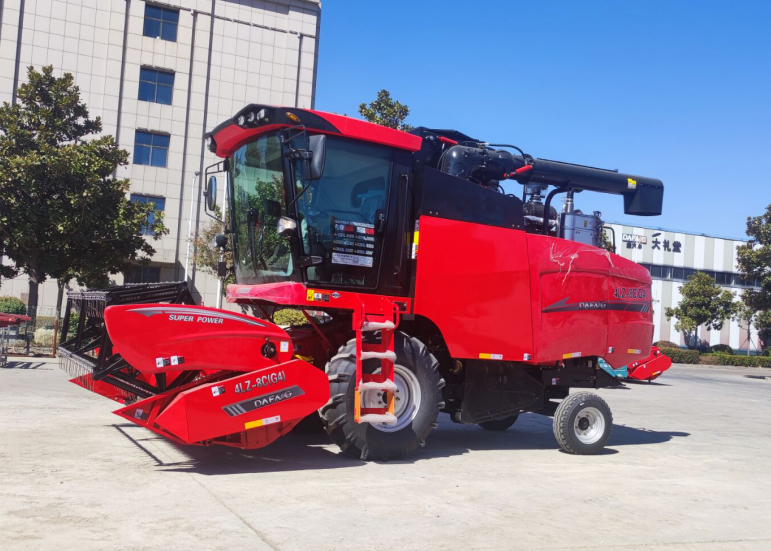
combine harvester
Full-feed Combine Harvester
When using a full-feed combine harvester for harvesting, all the cut straw and grain heads go into the cylinder for threshing. Because it needs to process the straw, it consumes more power. However, the total grain loss rate can be as low as 3.5%, and the impurity rate is less than 2%.
A fully-fed combine harvesting machine has a relatively simple structure, featuring a reel and an auger. Additionally, driving a fully-fed combine harvesting machine doesn’t require lining up, making it faster and more versatile.
According to Walking Type
Based on the walking type, combine harvesting machines can be divided into wheeled and crawler types.
Wheeled Combine Harvester
Wheeled combine harvesting machines move using wheels, which keeps transportation costs low. However, they are not suitable for special road conditions. Wheeled harvesting machines have a stronger load capacity, a longer lifespan, and are easier and cheaper to repair. However, since they have a smaller contact area with the ground, they may impact the soil.
Crawler Combine Harvester
Tracked combine harvesting machines move using tracks and need a trailer for transportation, which makes costs higher. However, they can operate smoothly on hilly terrain, terraced fields, and muddy ground. They have a weaker load capacity, and maintenance costs are higher due to the complexity of the tracks.
According to the Driving Force
Based on the power drive method, combine harvesters can be divided into self-propelled, trailed, and mounted types.
Self-Propelled Combine Harvester
A self-propelled combine harvester has its own engine and transmission system, allowing it to move and operate independently. All the power needed for moving, harvesting, threshing, and cleaning comes from its built-in engine.
Because it carries its own power system and has a compact structure, the self-propelled harvester can move flexibly in the field without relying on external traction or mounting equipment. Its self-propelled design enables efficient and continuous operation, helping you save time otherwise lost in repositioning or adjustments.
This type of harvester is widely used and suitable for various terrains and crop types, especially for large, continuous farmland.
Mounted Combine Harvester
A mounted combine harvester is attached to a tractor or a self-propelled chassis. Based on the way it is mounted, it can be divided into fully mounted and semi-mounted types. In a fully mounted harvester, the entire weight of the cutting platform and threshing unit is supported by the tractor. In a semi-mounted type, part of the weight is supported by the tractor, while the rest is supported by the harvester’s own wheels.
This type of harvester mainly consists of a cutting platform, conveyor trough, threshing and separation units, and the mounting system. Its structure is simple, and the cost is low. It makes full use of small and medium-sized tractors and doesn’t occupy the power and drive system all year round. After the harvest season, all harvesting components can be removed, and the tractor or chassis can be used for other tasks. This keeps the overall machine price and operating cost low.
Mounted combine harvesters are best suited for small and scattered fields. They are flexible with different row spacings and can handle crops planted with varying row widths. However, they require specific tractor configurations for mounting, which makes them less convenient than trailed machines. In addition, operator visibility is often limited.
According to the Direction of the Threshing Drum
According to the direction of the threshing drum, it can be divided into tangential flow and axial flow combine harvesters.
Tangential-flow combine harvester
A tangential flow combine harvester refers to a harvester where the threshing drum is perpendicular to the direction of machine movement, hence it is also known as a transverse flow combine harvester. After the crops enter the machine, the straw and grains quickly pass through the threshing drum along the tangent direction of the drum, relying on the impact and rubbing of the drum teeth to complete the threshing. The crops that are not completely removed continue to pass through the separation device, and finally enter the cleaning screen and fan to complete the separation of grains and impurities. The structure of the shear-type combine harvester is relatively simple, the manufacturing cost is low, the maintenance is convenient, and the requirements for field plots are not high. It can operate in small plots and complex terrains, and is suitable for small and medium-sized agricultural machinery users.
Axial flow combine harvester
Axial flow combine harvester, also known as longitudinal flow combine harvester, is a type of harvester where the threshing drum is parallel to the direction of machine movement. Its drum is usually relatively long. After entering the machine, crops enter the drum in a spiral direction and are subjected to rubbing, kneading, friction, and impact for a long time, gradually completing the separation of seeds and straw. Due to the long drum and large separation area, the vast majority of seeds can be separated inside the drum, and the remaining ones are processed through screening and air selection systems. Axial flow combine harvester has thorough threshing, low grain damage rate, large separation area, strong processing capacity, and can meet the needs of large-scale continuous operation of high-yield crops and crops with high requirements for grain cleanliness. It is very suitable for harvesting rice and soybeans.
Key Considerations When Choosing a Combine Harvester
When you want to buy a combine harvesting machine, you might feel overwhelmed by the many types available in the market. You can consider the following factors to help you make a decision.
Crop Type
This article discusses rice and wheat combine harvesting machines. As the name suggests, you can use these harvesting machines to harvest rice and wheat. However, they can also use fully-fed combine harvesting machines for barley, canola, and soybeans, which have shorter stems. If you grow these crops, you might want to choose a fully-fed model.
Performance Requirements
If you value the breakage rate of grains, the cleanliness of cleaning, or harvesting high moisture crops, you can prioritize axial flow grain combine harvesters. Axial flow combine harvesters have strong versatility and can harvest a variety of crops by replacing the cutting head. If your crop variety is relatively single, not grown on a large scale, and your budget is not high, then you can prioritize the use of a cutting flow combine harvester, which has a simple structure and lower maintenance costs, and difficulties in the later stage.
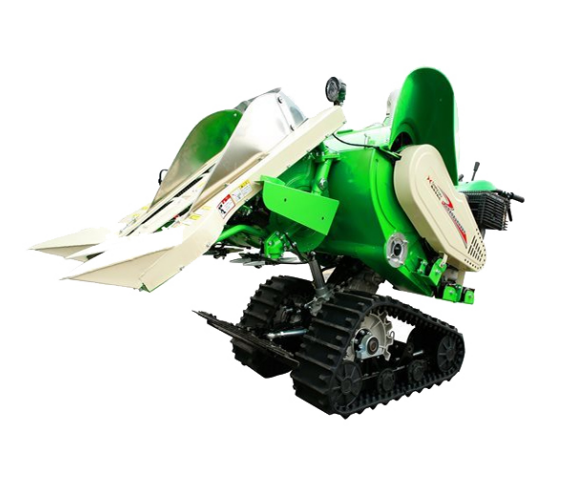
small self-propelled combine harvester
Field Size and Terrain
If you are working in hard soil, you can choose a wheeled combine harvesting machine. If the land is muddy, I recommend using a crawler combine harvesting machine to avoid getting stuck.
Not all combine harvesting machines are large. If your fields are not very big or if you are working in hilly or mountainous areas where big machines can’t go, you can choose a small self-propelled combine harvesting machine. It perfectly solves this problem.
Grain Tank Capacity
Moreover, the capacity of the grain bin is also an important factor to consider. A larger grain bin allows for longer working time and fewer unloading trips, helping you reduce fuel consumption.
Wrap Up
In sum, I have shared a lot of information about combine harvesting machines, and I hope you understand them better now than before reading this article. If you need help with purchasing, feel free to contact us at ANON. We are happy to provide you with professional assistance!
FAQ
What are the advantages of a combine harvester?
- Save labor
- Save time
- Higher efficiency
- Can complete multiple tasks at once
- Reduce harvesting costs